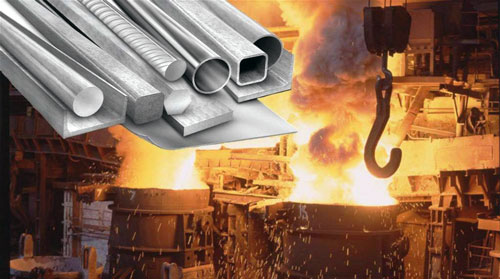
Твёрдость металлов
Твёрдость металла — это способность его сопротивляться проникновению в него другого, не получающего остаточных деформаций, тела.
Наиболее распространённые способы испытания твёрдости металлов, применяемые на заводах, можно разделить на две группы:
- испытание медленно нарастающей (статической) нагрузкой (твёрдость по Бринелю и по Роквеллу);
- испытание динамически действующей нагрузкой (твёрдость по Шору).
Твёрдость по Бринелю определяется путём вдавливания в испытуемый образец шарика диаметром D (в мм) из закалённой шарикоподшипниковой стали на прессе типа Бринеля. С помощью специальной лупы измеряется диаметр d (в мм) лунки и по специальным таблицам определяется число твёрдости. Это число представляет собой частное от деления величины нагрузки (в кГ) на площадь поверхности сферического отпечатка (в мм²). Чем больше отпечаток, тем мягче металл, и наоборот. Шарики применяются диаметром 10, 5 и 2,5 мм. При измерении твёрдости шариком диаметром 10 мм под нагрузкой 3000 кГ с выдержкой 10 сек. перед числом твёрдости пишется обозначение НВ, например так: НВ 190, т. е. твёрдость по Бринелю 190. При других условиях измерения обозначение НВ дополняется индексом, указывающим условия измерения в следующем порядке: диаметр шарика — 90 кГ. Следовательно, общая нагрузка соответственно будет: 150, 60 или 100 кГ.
Значения твёрдости определяются по разности глубин вдавливания алмазного конуса или шарика под действием общей нагрузки (глубина h) и предварительной (глубина Л) и отсчитываются по шкалам индикатора. Всего прибор имеет три шкалы: Д В и С.
Определение твёрдости закалённых деталей и инструментов производят алмазным конусом при общей нагрузке 150 кГ и отсчет ведут по шкале С. В этом случае перед числом твёрдости пишется обозначение HRC (твёрдость по Роквеллу, шкала С). Например, твёрдость режущих инструментов из быстрорежущей стали равняется 60—65 единицам по Роквеллу и обозначается HRC 60—65 или просто RC 60-65.
Определение твёрдости очень твёрдых металлов (более RC 70), твёрдых сплавов, минералокерамики, а также тонких пластин или тонких (0,3—0,5 мм) поверхностных слоёв производят алмазным наконечником при общей нагрузке 60 кГ и отсчёт ведут по шкале А В этом случае перед числом твёрдости пишут HRA или RA. Например, металлокерамические твёрдые сплавы имеют твёрдость RA 88—91, а режущие пластины из минералокерамики — твёрдость RA 90—93.
Стальным шариком при общей нагрузке 100 кг определяют твёрдость мягкой (отожжённой) стали или цветных сплавов. В этом случае перед числом твёрдости пишут HRB или RB.
твёрдость металлов по Шору определяют по высоте, на которую подскакивает боек с алмазным наконечником, падающий на испытуемую поверхность с определённой высоты. Чем больше высота отскока бойка, тем меньше работа пластической деформации материала, т. е. тем выше твёрдость. Чаше всего этим способом определяют поверхностную твёрдость шлифованных изделий. Преимущество этого способа испытания перед другими заключается в том, что на испытуемой поверхности остаётся лишь небольшой след бойка.
Зная твёрдость металла по Бринелю {НВ), можно находить приближенное значение его предела прочности при растяжении (Рь) по формулам
Имеется также определённое соотношение между числами твёрдости по Бринелю, Роквеллу и Шору. Так, твёрдость различных металлов (закалённых и незакалённых, кроме мягких) колеблется в пределах: по Бринелю НВ 160—780, по Роквеллу JRC 1—70 и по Шору 26—106.
Технологические свойства металлов
Характеристики металла, определяющие его способность подвергаться формообразованию различными методами, составляют вместе комплекс технологических свойств. Эти свойства должны учитываться как конструктором, назначающим марку материала для той или иной детали машины или прибора, так и рабочим, непосредственно осуществляющим изготовление данной детали.
Для процессов, осуществляемых в заготовительных цехах (литейный, кузнечный, сварочный), решающее значение имеют такие свойства металлов, как способность в расплавленном состоянии заполнять рельеф литейной формы (жидкотекучесть), способность в горячем состоянии изменять свою форму под ударами молота или под давлением пресса, способность свариваться и т. п.
Так, чугуны, обладая достаточной жидкотекучестью, хорошо заполняют литейную форму, тогда как стали при заливке ведут себя в этом отношении хуже и, остывая быстрее чугунов, склонны к образованию усадочных и газовых раковин. Стали компании https://specmetall.su/, однако, хорошо поддаются ковке, тогда как обычные чугуны этой операции подвергаться не могут. В отличие от чугунов стали, и прежде всего низкоуглеродистые, хорошо поддаются сварке.
Для процессов, осуществляемых в механических цехах, решающее значение имеет способность металла подвергаться обработке снятием стружки. Эта способность характеризуется понятием обрабатываемость.
Обрабатываемость — понятие комплексное. Оно охватывает совокупность нескольких технологических свойств материала, характеризующих его влияние на следующие стороны процесса резания:
- относительный уровень скоростей резания, с которыми целесообразно производить обработку данного материала;
- относительные величины сил и мощности, затрачиваемые при осуществлении процесса резания;
- возможность получения хорошей чистоты обработанной поверхности на отделочных операциях и степень дробимости стружки.
Очевидно, допустимый уровень скоростей резания трубы ст 12х1мфсамым непосредственным образом определяет производительность и стоимость механической обработки. Относительные величины сил и мощности, затрачиваемые на резание, существенно влияют на выбор оборудования и режущего инструмента, а также на расход электроэнергии.
Высокая степень чистоты обработанной поверхности необходима для всех участков детали, которые в сборочной единице сопрягаются с другими деталями и прежде всего — на трущихся поверхностях. В ряде случаев для получения чистой обработанной поверхности заготовку приходится подвергать специальной термической обработке. Так, сталь 12х1мф с этой целью часто подвергается нормализации.
Большое значение (при работе на токарных и сверлильных станках), особенно в условиях автоматического производства, имеет степень дробимости стружки. Отвод сливной стружки из рабочей зоны может оказаться настолько затруднительным, что автоматизация обработки будет невозможна.
Отечественной металлургической промышленностью выпускаются особые, так называемые автоматные стали, используемые для изготовления различного рода мелких неответственных деталей на токарных автоматах. Повышенное против обычного содержание серы и фосфора в этих сталях обусловливает образование сульфидов и фосфидов, прерывающих сплошность металлической основы стали, благодаря чему стружка легко ломается в самый момент ее образования.
Правильный учет технологических свойств материалов позволяет достигнуть заметного снижения затрат времени на обработку и таким образом снижения себестоимости изделия.
Чугуны
В связи с технологической сложностью получения ковкого чугуна количество отливок из него не превышает 3—5% от общего количества чугунного литья в машиностроении. Марки ковкого чугуна обозначаются буквами КЧ (ковкий чугун) и цифрами. Например, КЧ 45-6 обозначает: ковкий чугун с пределом прочности при растяжении 45 кГ/мм² и относительным удлинением 6%.
Легированный чугун представляет собой обычный серый чугун, в котором содержатся примеси других металлов, хром, никель, молибден, ванадий, медь и др. Эти примеси улучшают механические свойства чугуна, повышают стойкость против коррозии и истирания, из легированного чу-на изготовляют коленчатые валы, блоки и головки цилиндров, гильзы и другие ответственные детали.
Обрабатываемость чугунов хуже обрабатываемости сталей. Объясняется это тем, что чугуны характеризуются плохой теплопроводностью и наличием твёрдых включений, а на поверхности отливок всегда имеются остатки формовочных смесей, оказывающих абразивное (истирающее) действие на режущие инструменты.
Обрабатываемость чугуна резко ухудшается при наличии твёрдой отбеленной наружной корки, а также в результате очистки отливок в барабанах, которая приводит к заметному упрочнению поверхностного слоя (наклёту).
Стали
Основным свойством стали является её способность закаливаться. Чем больше углерода содержит сталь, тем выше её прочность, твёрдость, упругость и способность закаливаться и тем ниже ковкость и свариваемость.
Углеродистые стали принимают закалку при содержании углерода от 0,35% и выше. Легированные стали, в зависимости от содержания легирующих элементов, могут хорошо воспринимать закалку при содержании углерода от 0,17%.
По химическому составу стали разделяются на углеродистые и легированные. Последние кроме железа и углерода содержат один или несколько таких химических элементов, как хром, вольфрам, никель, ванадий и пр. Эти элементы повышают показатели механических свойств стали, а также сообщают ей особые свойства, например устойчивость против истирания, коррозии и т. п.
Углеродистые стали делятся на конструкционные и инструментальные, а легированные — на конструкционные, инструментальные и специальные.
Углеродистая конструкционная сталь изготовляется обыкновенного качества и качественная.
Сталь углеродистая обыкновенного качества (ГОСТ 380-60) применяется в машиностроении для изготовления деталей неответственного назначения и в строительных металлических конструкциях; обозначается буквами Ст. с добавлением номера стали. Стандартом установлено восемь марок этой стали: Ст. 0, Ст. 1, Ст. 2, Ст. 3, Ст. 4, Ст. 5, Ст. 6, Ст. 7.
Чем выше марка стали, тем больше в ней содержится углерода и тем она прочнее. Например, сталь марки Ст. 1 содержит 0,06—0,12% С (углерода) и ее предел прочности при растяжении 32—40 кГ/мм², а сталь марки Ст. 7 содержит 0.50—0.62 % С и её предел прочности 70—74 кГ/мм² и более.
Детали из стали по ГОСТ 380-60 обычно не подвергаются термической обработке.
Сталь углеродистая качественная струкционная (ГОСТ 1050-60) применяется для более ответственных деталей разделяется на две группы: с нормальным содержанием марганца (до 0,8%) и с повышенным содержанием марганца (марганцовистая).
Стали первой группы обозначают двузначным числом, указывающим среднее содержание углерода (в сотых долях процента). Например, сталь 15 содержит в среднем около 0,15% С; сталь 40—около 0,40% С.
ГОСТ 1050-60 предусматривает следующие марки конструкционной стали с нормальным содержанием марганца: 10; 15; 20; 25; 30; 35; 40; 45; 50; 55; 60; 65; 70; 75; 80; 85.
Для обозначения сталей второй группы (марганцовистых) добавляется буква Г' Например, 15Г; 20Г; 25Г; 30Г; 35Г; 40Г; 45Г; 50Г; 60Г; 65Г; 70Г.
Если содержание марганца превышает 1%, то после буквы Г ставится цифра, указывающая приблизительное содержание марганца в процентах. Например: 35Г2 — сталь с содержанием углерода около 0,35% и марганца около 2%.
Сталь конструкционная легированная (ГОСТ 4543-61) содержит кроме углерода и марганца присадки других металлов — хрома, никеля, молибдена, ванадия и пр., изменяющие свойства стали в соответствии с теми или иными требованиями. Применяется преимущественно в автомобильной и тракторной промышленности, в приборостроении, авиастроении и др. для изготовления деталей ответственного назначения. Легированные стали обозначаются марками, состоящими из двузначных чисел, которые указывают среднее содержание углерода (в сотых долях процента), и указывающих основные легирующие садки:
В — вольфрам, Н — никель, X — хром, Г — марганец, С — кремний. Ф — ванадий, М — молибден, А — алюминий;
Например, марка 20ХН означает хромоникелевую сталь с содержанием углерода около 0,20%, марка 15ХФ — хромованадиевую сталь с содержанием углерода около 0,15%.
Если содержание присадки превышает 1%, после соответствующей буквы ставится цифра, указывающая процентное содержание элемента.
Например, 12ХНЗ — хромоникелевая сталь с содержанием никеля около 3% и углерода около 0,12%.
Для обозначения высококачественных сталей, особо чистых в отношении вредных примесей (серы, фосфора) к марке стали добавляется буква А.